The Stud Welding Process
The Benefits of Stud Welding
It’s impossible to mention arc shields without the stud welding method and its benefits. Stud welding is the process of joining a fastener, or stud, to a base metal or substrate by heating both parts with an electrical arc and applying force. The fusion created at the cross-section of the arc welded metals is stronger than the metal surface or stud would be alone. Unlike riveted fasters, stud welding requires no holes. This prevents the weakening of the integrity of a structure. The lack of drilling also makes arc welding a simpler, faster process that doesn’t blemish the surface.
Additional Benefits
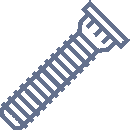
Can weld nearly any size
and type of stud
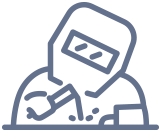
A finished arc weld is
stronger than the stud
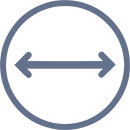
Diameter up
to 1-1/4″
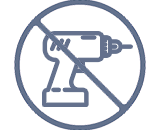
No drilling necessary
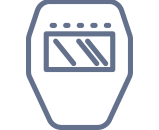
Structural-type strength weld
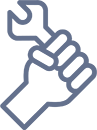
Reduced labor costs
The Arc Stud Welding Method
Stud welding requires the use of an arc shield (ferrule). The ceramic ring concentrates the heat generated from the welding gun, prevents oxidation, and retains the molten metal in the weld zone. Arc shields are single-use.
- The stud and the ceramic arc shield are placed in the gun and pressed against the work plate.
- The trigger is squeezed, igniting the arc, which melts the end of the stud and the work area.
- The arc shield concentrates the heat before the gun forces the stud into the molten metal.
- Once cool, the welder breaks the arc shield away, exposing the weld fillet around the stud base.
Our Arc Shield Manufacturing Process
Dynamic Ceramics creates 99% of our products in-house. This allows unparalleled control over the quality and customizability of our arc shields.
- Clay in raw materials form is shipped in from all parts of the country
- Clay is mixed and dried in our mixing department
- Clay is formed into specific parts in our press department
- Parts in greenware form are loaded onto cars and fired in one of our kilns in our kiln department
- Finished parts are then packed into boxes, wrapped, and ready to ship from our shipping department